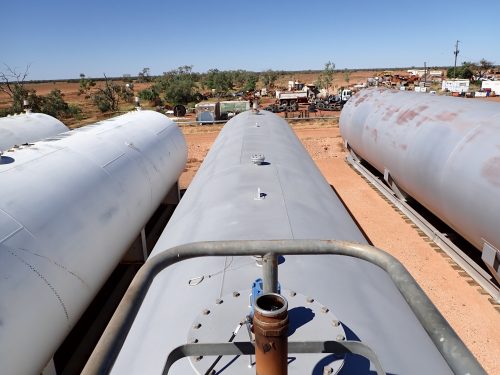
Vertech understands that bulk storage tanks are assets of both strategic and operational importance for companies across a large range of industry sectors. Our specialised range of storage tank inspection services assists our customers in maintaining their tank inspection activities and maintenance and repair schedules to ensure maximum availability while complying with Australian Standards and EPA requirements.
Our clients benefit from our team of experienced API-653 tank inspectors and engineers who can evaluate the inspection data, perform remnant life calculations, design weld repairs and prepare weld procedures.