In 2021, Vertech delivered the inspection services for Santos’s Gladstone LNG plant turnaround. The scope included inspection engineers, advanced NDT, rope access, in-service inspection of pressure equipment, and remote digital visual inspection (RDVI) teams.
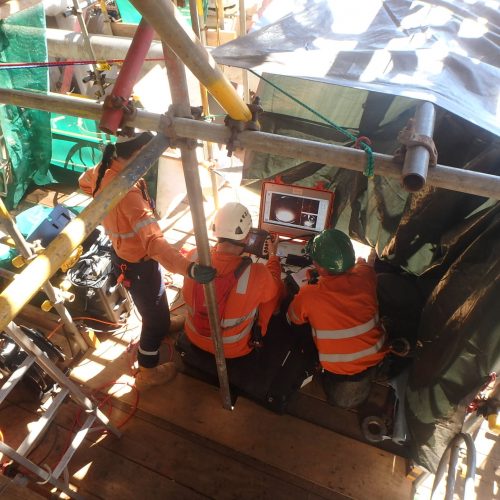
GLNG Turnaround
The turnaround was delivered safely and to a high standard, with exceptional client feedback on the execution.
Pre-Shutdown Work
Review inspection work packs to determine inspection scope requirements for labour and equipment; estimate all equipment and labour hours; provide detailed RDVI, CVI, and NDT work packs that include scaffold and lagging requirements; and organise all equipment and specialist inspection personnel for mobilisation to the Site.
Scope of Work
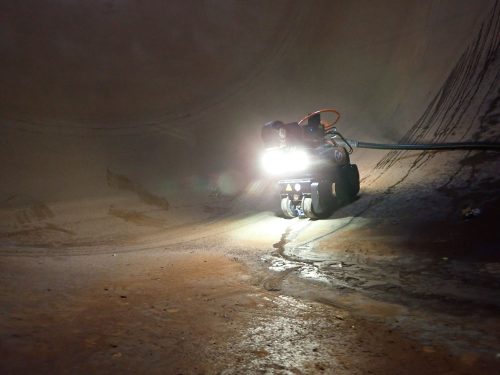
Vertech completed the based scope of work and identified several additional inspections during the shutdown. Our teams of AICIP, NDT, rope access, advanced NDT, tube inspectors, and RDVI inspectors completed inspections on time, on budget and with an exceptional safety record:
- 8 yearly internal and external inspection of hot oil trim cooler and pipeline gas preheater
- 5 yearly internal and external inspection of 4 lean solvent coolers.
- 8 yearly internal and external inspection of HP and LP fuel gas ko drum absorber ethylene purger condenser section.
- 8 yearly internal and external inspection of hot oil surge drum and fuel gas heater lean solvent cooler.
- 8 yearly internal inspection of ethylene purger absorber section and surge drum.
- 8 yearly internal and external inspection of propane purger adsorber section, refrigerant accumulator and purger condenser sections.
- 8 yearly internal and external inspection of 2 l.s. propane-ethylene condenser feed chillers.
- 8 yearly internal and external inspection of i.s. propane-methane, ethylene feed chiller.
- 8 yearly internal and external inspection of h.s. propane - methane and ethylene chiller.
- 8 yearly internal inspection of 2 regeneration gas heaters.
- 8 yearly internal and external inspection of de-gassing, solvent regenerator reflux and solvent flash drums.
- 8 yearly internal and external inspection of solvent regenerator.
- 4 yearly internal inspection of co2 absorber.
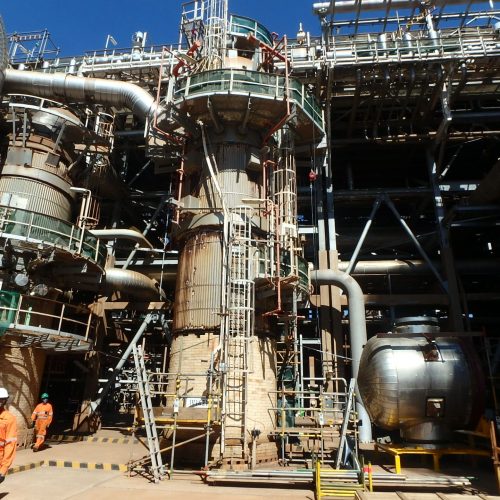
- 8 yearly internal and external inspection of ethylene compressor discharge cooler.
- 4 yearly internal inspection of 2 regenerator reboilers.
- 8 yearly internal and external inspection of 2 low stage propane suction drums.
- 8 yearly internal and external inspection of regeneration gas cooler.
- 8 yearly internal and external inspection of h.s. propane - feed chiller.
- 4 yearly internal inspection of dryer feed ko drum.
- 8 yearly internal and external inspection of 2 mercury removal beds.
- 8 yearly internal and external inspection of 3 molecular sieve dehydrators.
- 4 yearly internal/external inspection of hot oil start-up heater.
- 2 yearly internal inspection of waste heat recovery units x2.
- 8 yearly internal and external inspection of condensed water collection tank.
- 8 yearly internal and external inspection of ethylene compressor discharge cooler, intercooler, ethylene compressor and disch. coolers.