Vertech provided project management, coordination, and planning services in partnership with Woodside Energy’s EPCM Wood to deliver the GWA flare tip changeout. Using a custom flare tip handling package, our IRATA rope access, rigging, mechanical, and coatings teams replaced the flare tip located 160m above sea level (120m above deck) on a vertically designed flare tower.
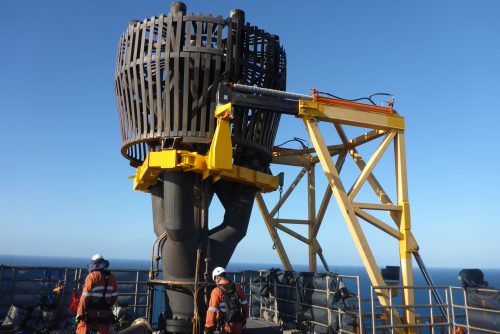
GWA Flare Tip Change
In addition to the flare tip replacement, Vertech specialist maintenance personnel completed the replacement of Nav Aids, Belzona repairs of critical structural members, NDT inspections, visual inspections, developed coatings procedures, and installed adhesion testing.
Introduction:
The Goodwyn Alpha Life Extension (GLE) project is an ongoing project to extend the life of the Goodwyn platform, its associated wells, risers, and subsea infrastructure until its end of economic life. The project’s objective is to extend the design life by 12-18 years from 2025 to realise the production of existing reservoirs and the upcoming Greater Western Flank development.
The Goodwyn Alpha Flare Tip is a Safety Critical Element responsible for ensuring the safe disposal of gas and liquid hydrocarbons. As part of the GLE project, the platform’s HP/LP flare tip was due to be replaced in 2018. The flare tip was replaced in 1998 (with a 10-year design life).
A designed flare tip handling package and rope access rigging and lifting services were used to remove and replace the Flare tip located 160m above sea level and 120m above the deck on the vertically designed flare tower.
Due to Vertech’s past success with technically challenging projects, we were once again asked to work closely with Woodside’s EPCM to ensure that the Flare Tip replacement and remediation works on the Flare Tower were completed safely and without incident during a challenging shutdown window.
Key Services:
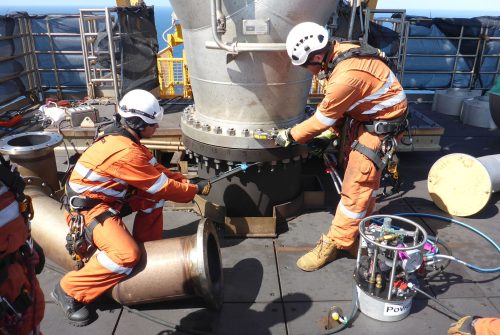
- Constructability Development
- Project Planning
- Risk Engineering Collaboration & Consultation
- Safe Work Methodology Development
- Rescue Scenario Development and Testing
- Rigging Plans
- NDT Competency Assessment
- Mechanical Fitting & Flange Management Competencies
- EEHA Electrical Inspection Trade
- Procurement and Logistics
Rope Access Solution
Early in the project, it was established that only Vertech rope access personnel would have access to the tower. Vertech personnel were required to be competent in the operation and fault finding of the 14t bespoke electric and hydraulic operating system so that in the event of system shutdown, rope access personnel could ensure project success.
The pre-shutdown access to the flare tower (lower levels) presented a unique challenge due to the potential radiant heat exposure in the event of a facility blowdown. Vertech provided equipment, a safe means of access, and an emergency escape plan specifically for this eventuality. This access for setting up equipment and tooling at lower levels of the flare tower ultimately provided an efficient lead-in to the shutdown scope of work.
Additional Services Provided:
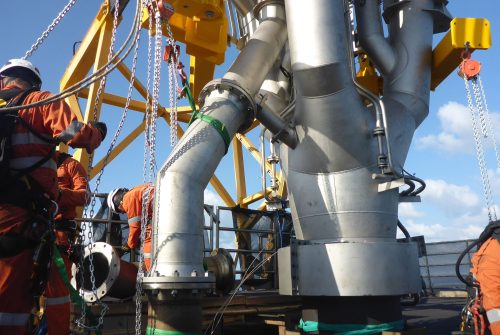
In addition to the Flare Tip replacement Vertech personnel also provided the following services on the flare tower within the same shutdown window:
- Removal and Replacement of Nav Aids
- Belzona Repairs of Critical Structural Members
- NDT and Visual Inspection
- Coatings Procedure Specification Development
- Coatings Procedure Qualifications
- Adhesion Testing
Project Execution:
On arrival, the team commissioned the Flare Tip Handling Package and function-tested the FTHP and all other Vertech equipment. This was followed by a ‘make safe’ campaign to remove potential dropped objects.
The FTHP was driven to the top of the flare, where our multi-disciplined rope access team used heavy rigging and lifting equipment to remove the flare tip. The operation was performed again to install a new flare tip and perform all the tensioning and torquing requirements.
There were a number of challenges in engineering, planning, and execution throughout this project. Through outstanding leadership, both onshore and offshore, this scope was successful and provided within timescales and under budget.